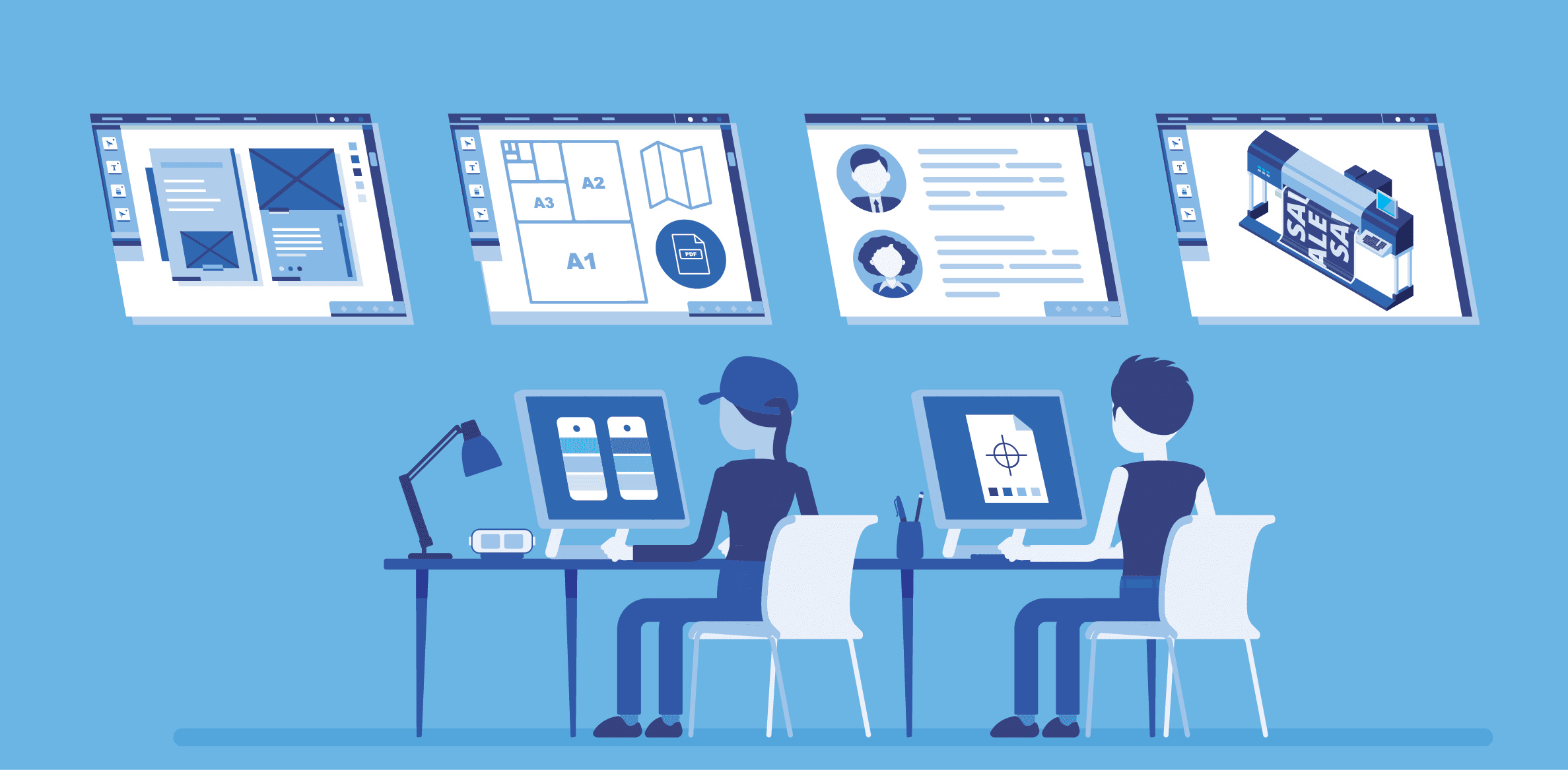
While the traditions of printing and their values have always inspired us at Meji, we have constantly evolved with changing needs and technology. Our first-hand experience of press and prepress makes us stand out among our competitors. Our unique Prepress Outsourcing service process is crafted to look after each aspect very carefully. We are Mac equipped with the required software to work with. We are able to handle jobs with any degree of complexity, providing press-quality PDF files that you only have to drag and drop to your CTP setter.
We are proud of our proven systems — especially of the fact that we have taken online prepress services to completely new heights. Data reception, Data Check, Compilation, Positioning, RIP, and the Internet how-about are the key aspects of our module. We work at zero time-lapse to turn around the task in the most efficient way. We are also open to redesigning your current process to make it more cost-efficient, leading to larger profits.
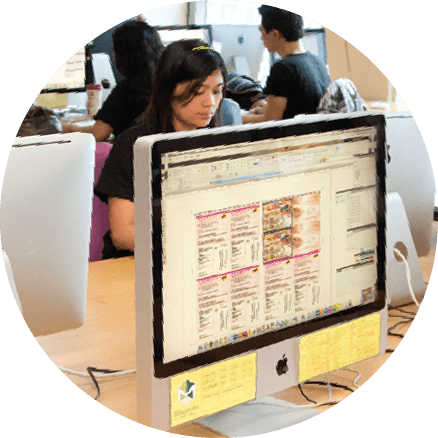
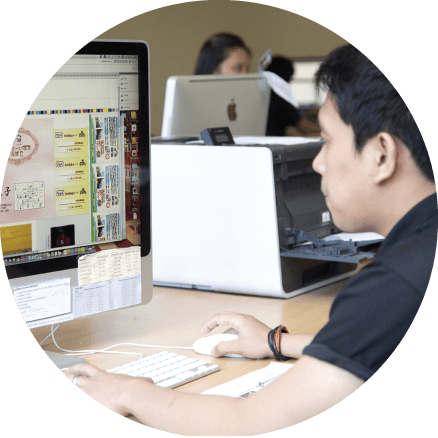
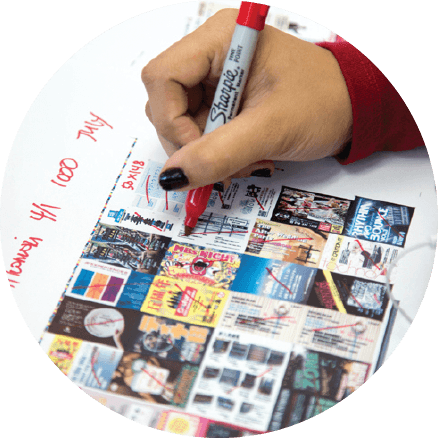
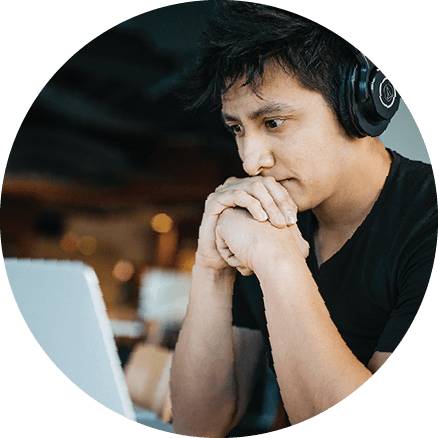
The Process
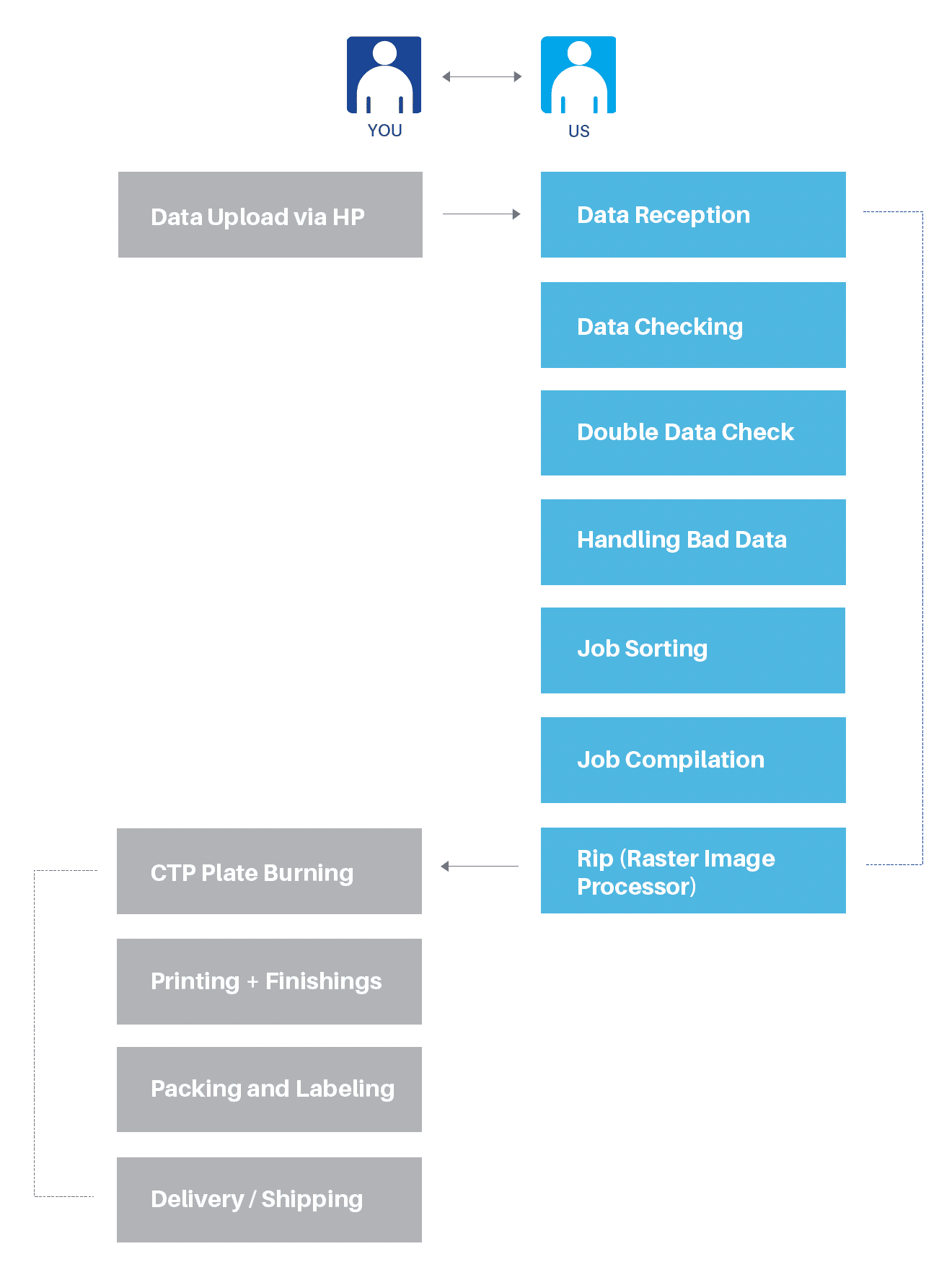
The Process Task
- Download and organize the data that is uploaded by your customers to your website/data server.
- Respond to or handle any issues with the customer over email programmed with your website.
- Issue an order placement sheet that is going to be attached to the data until it is shipped out of your printing factory
- Update the job progress to ‘Data Accepted’.
- We check the customer’s data for any errors. Mainly, we look into standard checks: size, colors, fonts outlined or not, links, bleed, cropmarks, typography cut or not, spot colors, overprint, after production folding, scoring, and attached sample jpeg files.
- If the data has no errors, we forward it to the next department attaching a jpg to the ‘PDF Order Sheet’ issued by the data receptionist, by making clear which data belongs to which order.
- We also move the job progress to ‘Data Checked’. If the customer’s data has any problem or it is not the same as the sample jpg the customers had presented with the upload, we consider it bad data and forward it to the ‘Bad Data’ section.
- Each data is checked before and after by the Data Checkers. This double check can detect any errors caused by the prepress staff or even the customer.
- In case the customer submits any data that is not printable for some reason, then we provide a screenshot pointing out the errors and we inform your customer via your data submission system.
- If the customer fails to resubmit the data on time, we will follow it up either on phone or mail, depending on the terms we agree upon at the initial contract.
- Each data is checked before and after by the Data Checkers. This double check can detect any errors caused by the prepress staff or even the customer.
- For the best efficiency and highest profit, we categorize the data into different job folders, keeping in mind the different printing aspects: size, paper options, printrun, number of copies, plate sizes, print machine schedule, and so on. This is key to building the incoming data into a cost efficient print job.
- We compile the sorted data into one printable A3 to B0 size layout, based on relevant press sizes, press specs and special post-press production tasks. We double check the final compilation for any possible left over errors.
- Using our superior quality Kodak Prinergy system, we do the four-colour separations and provide press-quality PDF files. You are only required to drag and drop it and let the plate roll out on your CTP setter.